Advanced Process Control Smart Manufacturing Conference 2021 in Review
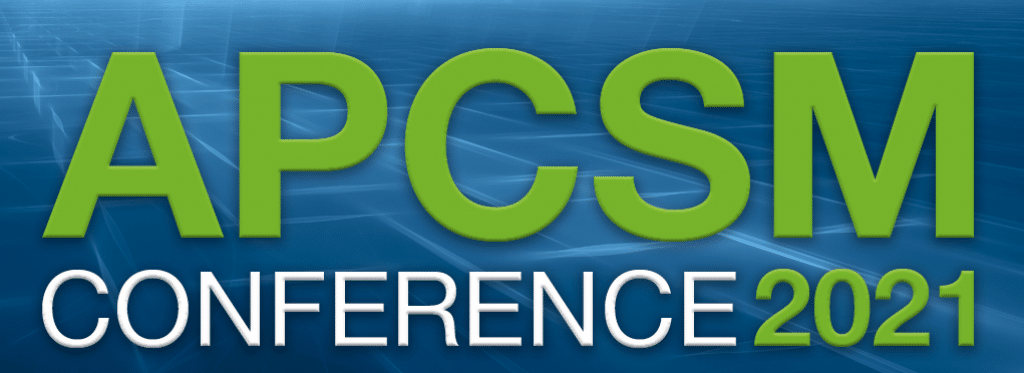
Last week I attended the APCSM 2021 virtual conference where thought leaders came together to share how Artificial Intelligence and Machine Learning are helping to meet current challenges in the semiconductor and related industries. Various talks shared how new strategies in run-to-run process control, fault detection and classification, predictive analytics, and virtual metrology enable improvements in yield, quality, and manufacturing efficiency. A summary of some of our key takeaways is presented below.
Run-to-Run (R2R) Process Control
Run-to-run process control is a strategy to modify run parameters using metrology feedback to maintain production specifications in face of process drift and disturbances. For example, a R2R controller could suggest modulating recipe parameters or modifying an overlay correction pattern for subsequent runs based on analysis of the error in previous runs. Established technology involves using a process model identified with design of experiments (DOE) to produce a linear model at the operating point, then modifying a constant term using an exponentially weighted moving average approach (EWMA). There is considerable promise in using a machine learning-based approach to enable robust R2R control in cases where linear+EWMA is inadequate. However, we observed talks where deep learning based R2R controllers failed to exceed the performance of the classic method. This demonstrates that ML based controllers must be carefully regularized and also specifically designed to aid in the cases where the classic approach fails: cases with inaccurate or changing process models or with high autocorrelation.
Fault Detection and Classification (FDC)
The process of timely fault detection (FD) and then understanding the type and cause of the fault or fault classification (FC) are core technologies required for maintaining good yield and process efficiency. The current sentiment is that although FD technology has already become quite mature, there is considerable opportunity in advancing FC systems to enable process engineers to be more efficient at fixing problems as they arise. Current FC strategies involve studying statistical process control charts, then comparing outliers with faults using univariate analysis. This strategy can be slow and tedious and also misses out on faults that occur due to non-linear relationships or complex multivariate interactions. Some presentations shared advances in multivariate FC techniques using machine learning (decision trees, PCA, SVMs, etc), using detailed analyses to give a hierarchy of most probable root causes for the fault. Key themes included using interpretable models to understand the origin for a fault and also using statistical methods to eliminate collinearity to return only the most relevant predictors. Another theme included using automatic trace segmentation to extract meaningful features from equipment time series data to use in FDC algorithms. Key challenges moving forward include making use of the time series data in FDC and designing FC systems that can identify both simple and complex root causes.
Predictive Analytics
A major industry trend is moving away from reactive FDC towards predictive analytics to prevent faults from occuring in the first place. Several talks shared examples of using ML to predict future behavior for use in failure prevention and preventive maintenance scheduling. One example showed that an ensemble model (an aggregate model composed of many simpler time series models) was able to quickly adapt to new behavior when deployed using on-line learning. Key challenges include using models that are robust enough to adapt to non-linear behavior without overfitting and giving false alarms, while making models lightweight enough to deploy on many different assets with efficient retraining.
Virtual Metrology
Another industry trend is using virtual metrology to reduce metrology costs and for earlier fault detection. Virtual metrology (VM) involves using a model to predict a metrology result in absence of the actual data, then using the VM prediction to take some action. A key theme was collaboration between data scientists and subject matter experts to identify relatively simple, interpretable models to use for VM. Important challenges in deploying VM solutions include effective MLOps (model monitoring and updating, etc.) with a lack of periodic collection of actual metrology results.
Summary
Although there is a considerable opportunity in leveraging AI in process control to unleash higher yields and more efficient processes in the semiconductor industry, there are practical challenges that must be overcome to realize the full potential. The presentation of these challenges validated the efforts of the Tignis team in developing our current technology suite. For example, our reinforcement learning process control (RLPC) has the ability to adapt the process model for more robust run-to-run control. Also, the surrogate modeling (SIM-AI) technology enables deployment of accurate machine learning models in cases where a large physical dataset is difficult to collect. Finally, our low-code digital twin query language (DTQL) empowers subject matter experts to develop effective predictive analytics and virtual metrology tools and deploy across many assets, with built in MLOps. Collectively, these tools have the capability to enable practitioners to overcome many of the aforementioned challenges.